Can Laser Welding Machines Replace Traditional Welding Methods?
How Laser Welding Machines Work
Core Technology Behind Laser Welding
At the heart of laser welding technology lies the use of highly concentrated light beams to precisely melt materials, creating strong and precise joints. The core technology can be divided into three essential components: the laser source, beam delivery, and focusing optics. Lasers operate on the principle of stimulated emission, producing a controllable and focused light energy. This allows for precision welding that stands apart from traditional welding methods, which often fall short in automation and quality assurance. The precise nature of laser welding has been a game-changer in industries that require high-quality welding results, such as automotive and aerospace.
Precision and Heat Control Mechanisms
One of the defining features of laser welding machines is their ability to control heat with precision, which minimizes the heat-affected zone (HAZ) and reduces thermal distortion. This precision ensures that only the necessary heat is applied, preserving the structural integrity of the components being welded. Advanced cooling systems and temperature sensors are integral to this process, monitoring and adjusting the heat levels in real time. These heat control mechanisms not only ensure consistent weld quality but also adapt efficiently to a variety of materials and thicknesses. The seamless integration of these systems is fundamental in maintaining high standards and consistent results in precision welding.
Integration with Fiber Laser Cutting Systems
Modern laser welding setups are often intricately connected with fiber laser cutting systems, resulting in enhanced manufacturing efficiency. This seamless integration reduces setup times significantly and allows manufacturers to switch effortlessly between welding and cutting functions. Such joint operations are adept at handling complex geometries while preserving accuracy across both processes. By enhancing overall productivity, this integration is invaluable in manufacturing environments that demand both precision and speed. This synergy between laser welding and fiber laser cutting highlights the technological advancements that drive improved performance in modern manufacturing practices.
Laser vs. Traditional Welding: Critical Comparisons
Speed and Process Efficiency Differences
Laser welding processes are remarkably faster than traditional methods, often reducing cycle times by up to 50%. This speed is crucial in industries such as automotive and electronics, where time is of the essence to meet production demands. Laser systems allow for continuous operation, facilitating unattended operation and maximizing productivity. The implementation of automation with laser systems further enhances efficiency, reducing manual intervention and minimizing human error in the welding process.
Material Compatibility and Weld Quality
One of the key strengths of laser welding is its effectiveness on a wide range of metals and materials, including those challenging to weld using traditional methods. The weld quality achieved through laser welding is typically superior, resulting in strong bonds and smoother finishes. Material thickness plays a role in selecting the appropriate laser type, as systems are available for both thin and thick materials. The high power density inherent in laser welding ensures minimal distortion, especially important for delicate components requiring precise and controlled welding.
Operator Skill Requirements
Unlike traditional welding techniques, operating laser welding machines generally demands less manual skill due to advanced automation features. While operators must undergo training, these programs are often shorter because of the intuitive design of laser systems. Consequently, operators can focus on process monitoring, rather than engaging in hands-on welding tasks. This shift in skill requirements is beneficial for manufacturing settings, supporting quicker onboarding and integration of new employees.
Voiern Laser Welding Machine Features
High-Energy Pulse Technology for Thin Materials
Voiern's laser welding machines utilize advanced high-energy pulse technology specifically tailored for the delicacies of welding thin materials. This technology ensures minimal thermal influence, thus preserving the substrates' integrity while delivering strong and reliable welds. Additionally, pulse control features offer finely-tuned energy delivery adjustments, accommodating the varying properties of different materials. Such refined control enables consistent high-quality joints throughout production, making Voiern machines ideal for industries where precision is non-negotiable.
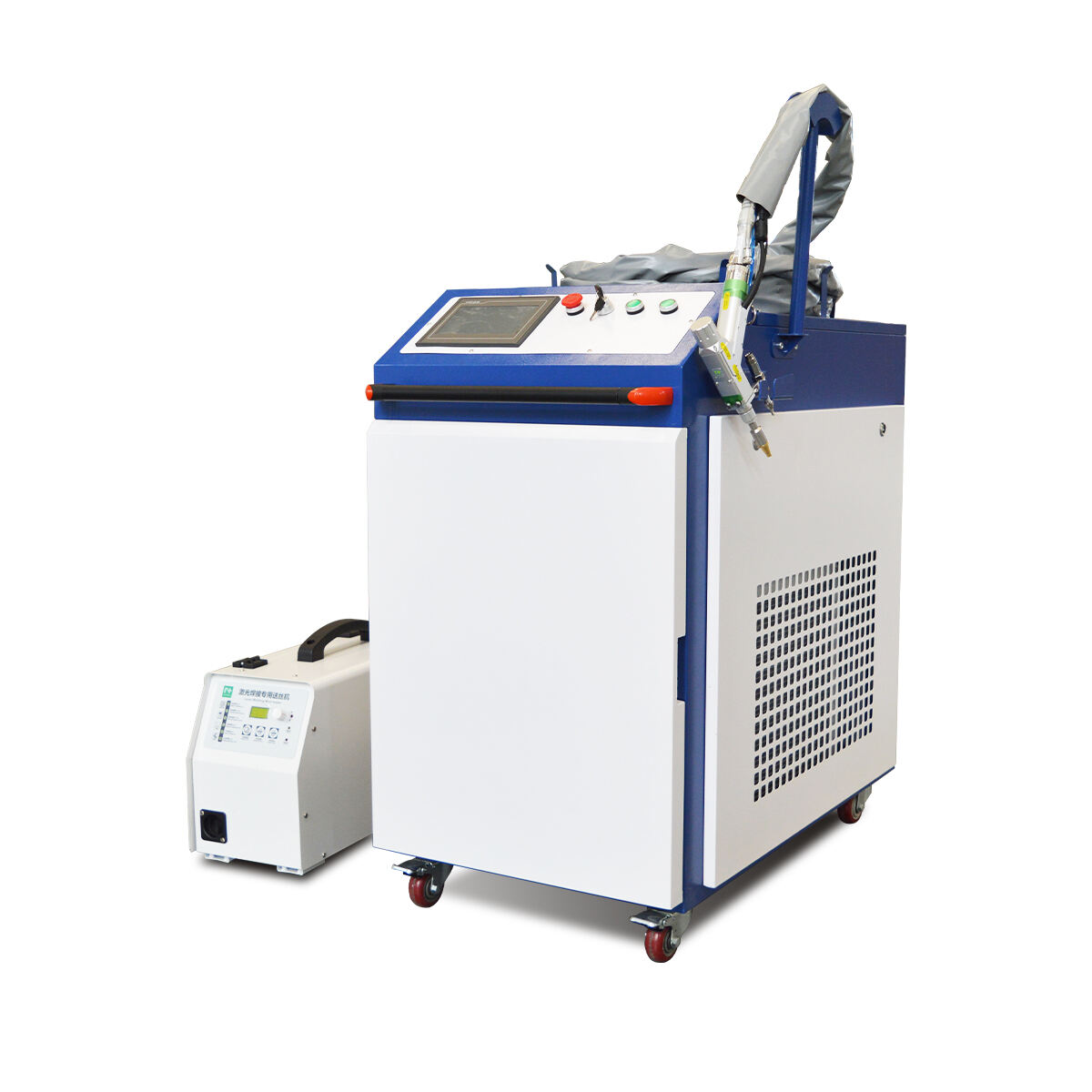
Automation-Ready Design and Seam Types
The automation-ready design of Voiern's laser welding machines facilitates seamless integration into existing production lines, enhancing workflow efficiency. With the ability to address various seam types—from butt to lap joints—these machines broaden their application capabilities, serving diverse industrial needs. A user-friendly interface simplifies programming, allowing for swift adjustments and reducing downtime. This integration of automated systems is pivotal in maximizing throughput and streamlining operations.
Technical Specifications and Certifications
Voiern's laser welding machines are equipped with comprehensive technical specifications that cover essential features such as power ratings, focal lengths, and operational speed, ensuring the suitability for various industrial applications. The machines are certified to meet ISO, CE, FDA, and SASO standards, highlighting their compliance with rigorous industry benchmarks critical for sectors like aerospace and medical. Comprehensive documentation detailing reliability, coupled with strong manufacturer support and post-purchase services, underscores the value Voiern offers, reinforcing buyers' confidence in investing in cutting-edge laser technology.
Industry Applications Driving Adoption
Automotive Component Manufacturing
Laser welding technology is pivotal in automotive component manufacturing, providing unmatched precision and durability that are essential in this industry. It is frequently utilized to join chassis, body panels, and exhaust systems, components that demand high durability. With the capability to weld various materials, including advanced alloys, laser welding surpasses traditional welding techniques, delivering robust and lightweight designs crucial for vehicle efficiency. Recent trends show a shift in the industry towards laser welding, driven by the need for lightweighting and enhanced fuel efficiency innovations in vehicle design. Reports indicate this shift is swiftly gaining momentum, positioning laser welding as a cornerstone technology in the automotive realm.
Medical Device and Electronics Production
In medical device and electronics production, precision is paramount, making laser welding an optimal solution for fulfilling industry demands. This technology excels in micro-welding capabilities, vital for fabricating small, intricate components found in these sectors. The adoption of laser welding is spurred by stringent quality and regulatory standards—requirements that laser technology seamlessly meets. Moreover, the potential for reduced contamination and improved cleanliness during the welding process makes laser welding exceedingly appealing, ensuring sterile environments which are particularly critical in medical device manufacturing. This confluence of benefits positions laser welding as a preferred choice in these industries.
Case Study: Precision in Aerospace Welding
Aerospace applications demand extraordinary precision, a demand that laser welding technology meets with its controlled heat input and fine accuracy. Case studies showcase substantial improvements in weld integrity and component reliability across various aerospace components. Critical examples include fuel tanks and engine components wherein any failure could lead to catastrophic consequences. Industries are increasingly leaning towards laser welding, recognizing its ability to reduce component weight while enhancing overall performance and safety. This technology's adoption is further boosted by its contribution to advancing aerospace technologies in a sector where precision engineering and component reliability are non-negotiable.
Economic Considerations for Manufacturers
Initial Investment vs. Long-Term Savings
Investing in laser welding technology may appear costly initially, but the long-term savings are substantial. Despite the upfront expenditure, cost analysis reveals that it significantly reduces material waste and the need for rework, which can drastically lower overall production costs. Many businesses experience a swift return on investment (ROI), especially those operating in high-volume manufacturing environments where efficiency is critical. By boosting productivity and minimizing downtime, total operational costs often decrease, eventually overshadowing the high initial expenses.
Reduced Post-Processing Costs
The precision of laser welding leads to fewer defects, markedly reducing the need for expensive post-processing. Its efficiency means less machining and polishing work is required after the weld is complete, saving time and labor costs. By minimizing the need for post-weld inspections, companies further cut down on labor and operational expenses. The enhanced weld quality offers more reliable products, leading to fewer returns and boosting overall customer satisfaction.
Market Growth and ROI Projections
The laser welding market is projected to expand significantly, fueled by increased demand across various industries. Companies investing in laser technologies are expected to gain a competitive advantage, with ROI projections suggesting rapid benefits. Industry reports indicate that adopting laser welding can result in substantial market share expansion. Staying ahead in technological advancements ensures that manufacturers remain competitive, sustainable, and ready for long-term success. The market dynamics, driven by innovation and demand, highlight the imperative for companies to integrate laser systems into their production processes.